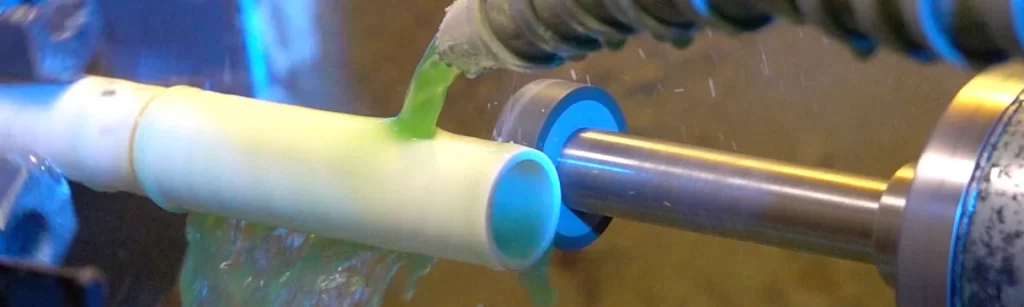
Machining and Grinding Advanced Ceramics & Performance Plastics
International Ceramic Engineering is an expert at diamond grinding and green machining of advanced ceramic materials. We also specialize in the custom fabrication of Performance Plastics.
Our machinists have experience and specific skills to meet your toughest advanced material requirements. We excel at producing complicated geometries and unique components at reduced costs. Our team of experts will assist you with the most cost effective design to ensure efficient and timely delivery of your advanced ceramic or performance plastic components.
International Ceramic Engineering is an expert at diamond grinding and green machining of advanced ceramic materials. We also specialize in the custom fabrication of Performance Plastics. Our machinists have experience and specific skills to meet your toughest advanced material requirements. We excel at producing complicated geometries and unique components at reduced costs. Our team of experts will assist you with the most cost-effective design to ensure efficient and timely delivery of your advanced ceramic or performance plastic components.
Technical ceramics, also known as advanced ceramics or engineering ceramics, are a class of materials that exhibit exceptional mechanical, thermal, and electrical properties. These ceramics include materials such as alumina (Al₂O₃), zirconia (ZrO₂), silicon carbide (SiC), and silicon nitride (Si₃N₄). Due to their hardness, wear resistance, and high-temperature stability, technical ceramics are increasingly used in a wide range of industrial applications, including aerospace, automotive, electronics, and medical devices. However, their unique properties also present significant challenges in machining and grinding processes. This white paper explores the methodologies, challenges, and advancements in the machining and grinding of technical ceramics.
Properties of Technical Ceramics
Mechanical Properties
- Hardness: Technical ceramics exhibit high hardness, often exceeding that of hardened steels. For instance, silicon carbide has a hardness of about 25 GPa on the Vickers scale, compared to 7-8 GPa for hardened tool steel.
- Wear Resistance: These materials are highly resistant to wear and abrasion, making them ideal for applications involving high friction and mechanical stress.
- Strength and Toughness: While generally strong, technical ceramics can be brittle and sensitive to flaws, leading to challenges in machining processes.
Thermal Properties
- High Temperature Stability: Technical ceramics maintain their mechanical properties at elevated temperatures, with some materials like silicon nitride being stable up to 1200°C.
- Thermal Conductivity: Materials such as silicon carbide exhibit high thermal conductivity, while others like zirconia have low thermal conductivity, offering a wide range of applications.
Electrical Properties
- Insulating and Conductive Ceramics: Technical ceramics can be either electrically insulating (e.g., alumina) or conductive (e.g., silicon carbide), catering to various electronic applications.
Challenges in Machining and Grinding of Technical Ceramics
Hardness and Brittleness
The extreme hardness of technical ceramics makes them difficult to machine using conventional methods. Additionally, their brittleness means they can crack or fracture under mechanical stress, necessitating precise and controlled machining processes.
Tool Wear
Machining and grinding tools experience significant wear when working with hard ceramics. This leads to frequent tool changes, increased downtime, and higher production costs.
Surface Quality
Achieving the desired surface finish and dimensional accuracy in technical ceramics is challenging due to their propensity for cracking and chipping during machining.
Machining Technical Ceramics
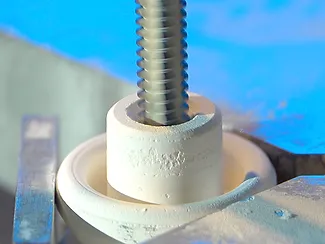
Diamond Grinding
Diamond grinding is the most common method for machining technical ceramics. Diamond, being harder than most ceramics, can effectively cut through the material. The process involves using diamond-impregnated grinding wheels to remove material through abrasive action.
Process Parameters
- Wheel Speed: Higher wheel speeds improve material removal rates but can also increase the risk of thermal damage.
- Feed Rate: Lower feed rates are typically used to minimize cracking and improve surface finish.
- Coolant: Coolants are essential to dissipate heat and prevent thermal damage to both the workpiece and the grinding wheel.
Laser Machining
Laser machining offers a non-contact method for cutting and shaping technical ceramics. High-energy laser beams are used to melt and vaporize the material.
Advantages
- Precision: Laser machining provides high precision and is capable of producing complex shapes.
- Minimal Tool Wear: As a non-contact process, there is no tool wear, reducing downtime and costs.
Limitations
- Thermal Damage: The high temperatures involved can cause thermal damage and induce microcracks in the material.
- Material Removal Rate: The material removal rate is generally lower compared to mechanical grinding.

Electrical Discharge Machining (EDM)
EDM is used for conductive ceramics such as silicon carbide. The process involves using electrical discharges to erode the material.
Advantages
- Complex Geometries: EDM is suitable for creating intricate shapes and fine details.
- Minimal Mechanical Stress: As a non-contact process, EDM minimizes mechanical stresses and reduces the risk of cracking.
Limitations
- Conductivity Requirement: EDM is limited to electrically conductive ceramics.
- Slow Process: The material removal rate is relatively slow, making EDM less suitable for large-scale production.
Advancements in Machining and Grinding for Technical Ceramics
Ultrasonic Machining
Ultrasonic machining combines high-frequency vibrations with abrasive slurry to machine technical ceramics. This process reduces mechanical stress and improves surface quality.
Benefits
- Reduced Tool Wear: The use of abrasives in a slurry reduces wear on the machining tool.
- Improved Surface Finish: The ultrasonic vibrations help achieve smoother surfaces and finer details.
Hybrid Machining
Hybrid machining techniques, which combine multiple processes such as laser-assisted grinding or EDM combined with conventional milling, are gaining popularity. These methods leverage the strengths of each process to overcome the limitations of individual techniques.
Automation and CNC Technology
Advancements in computer numerical control (CNC) technology and automation have significantly improved the precision and efficiency of machining technical ceramics. CNC machines can precisely control tool paths, feed rates, and other parameters to optimize the machining process.
Machining and grinding of technical ceramics are complex processes that require specialized techniques and equipment. The inherent hardness and brittleness of these materials present significant challenges, but advancements in machining technologies are continually improving the efficiency and quality of the processes. Diamond grinding remains the most common method, while laser machining, EDM, and ultrasonic machining offer viable alternatives for specific applications. As technology evolves, hybrid machining and automation are expected to play an increasingly important role in the machining of technical ceramics, enabling the production of high-precision components for a wide range of industries.
Tolerances and cost savings

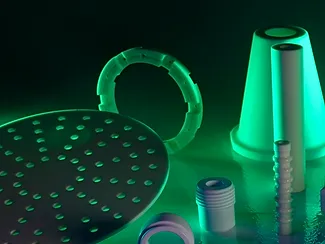
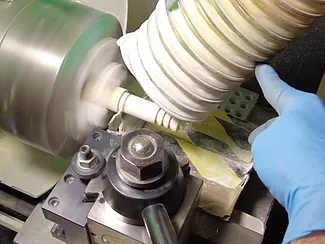
Why should you consider ceramics over metal?